Neodymium Magnet Catalogue
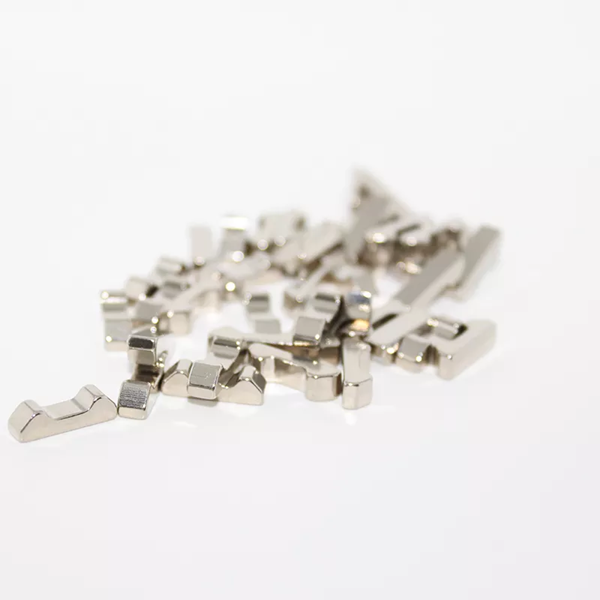
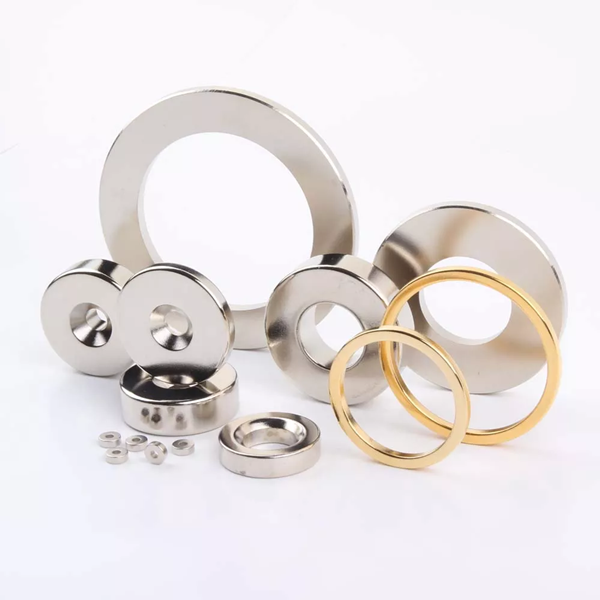
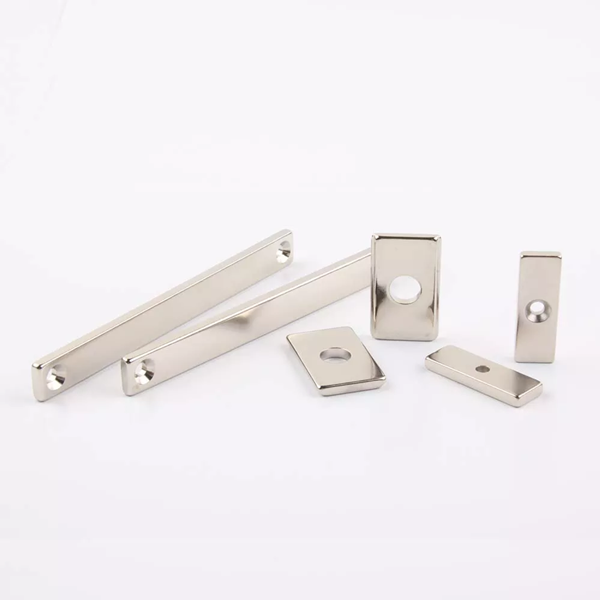
Neodymium magnet special shape
Ring shape neodymium magnet
NdFeB square counterbore
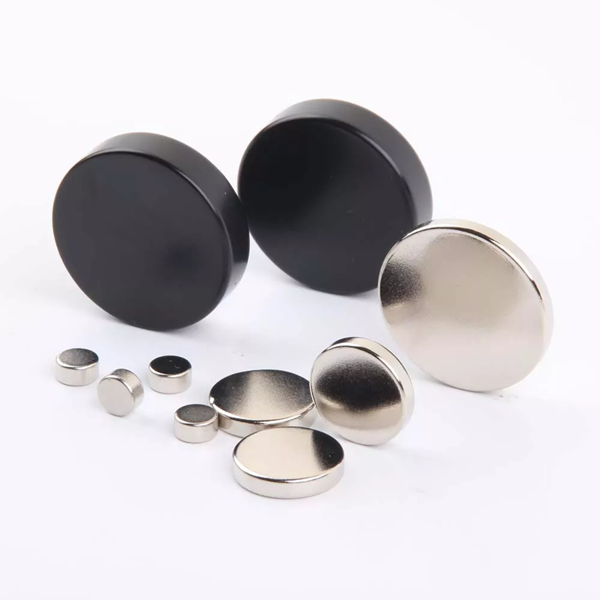
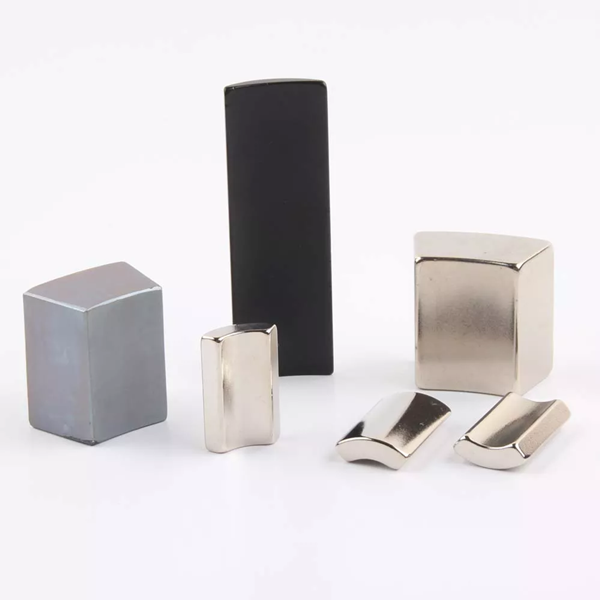
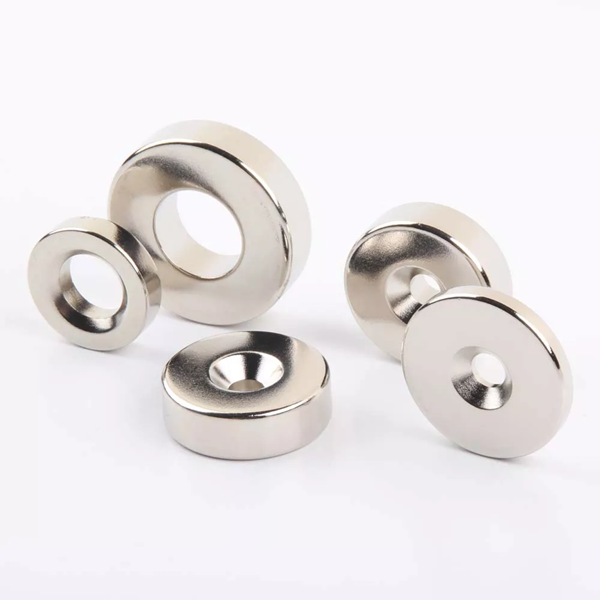
Disc neodymium magnet
Arc shape neodymium magnet
NdFeB ring counterbore

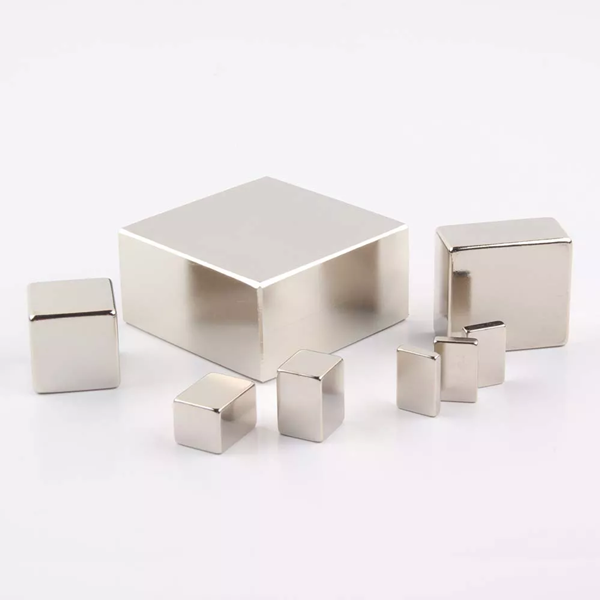
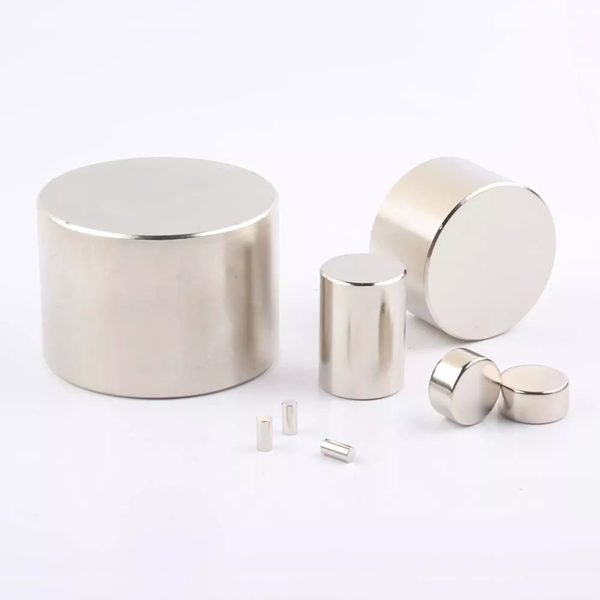
Rectangular neodymium magnet
Block neodymium magnet
Cylinder neodymium magnet
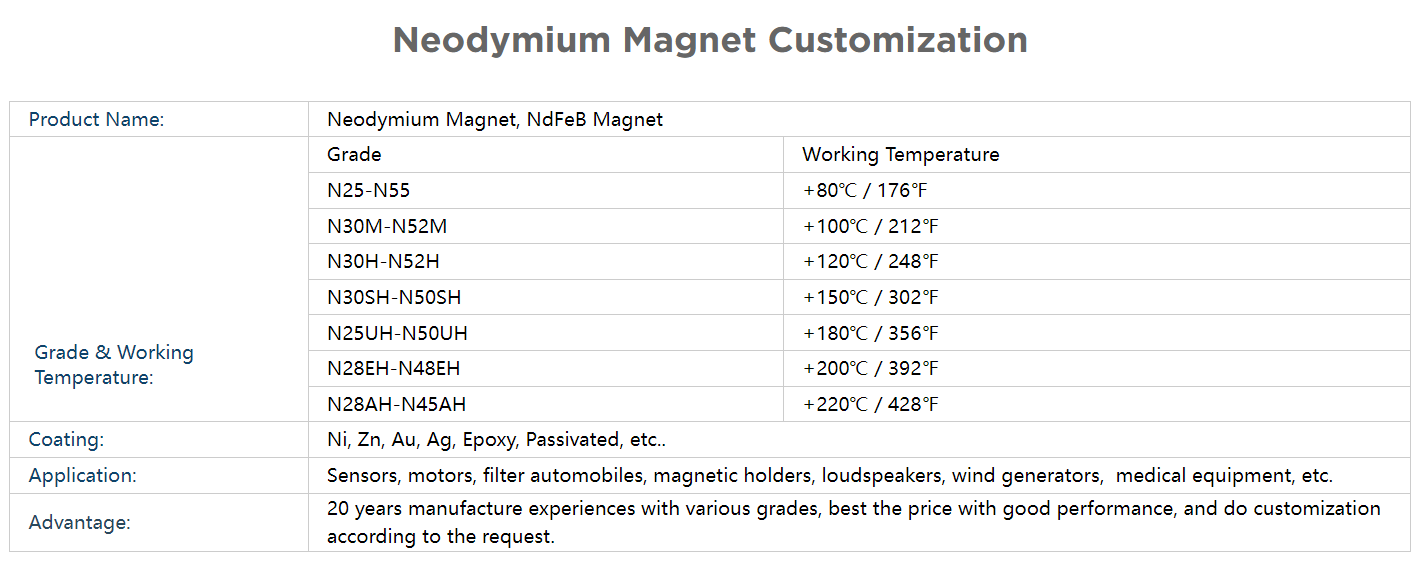
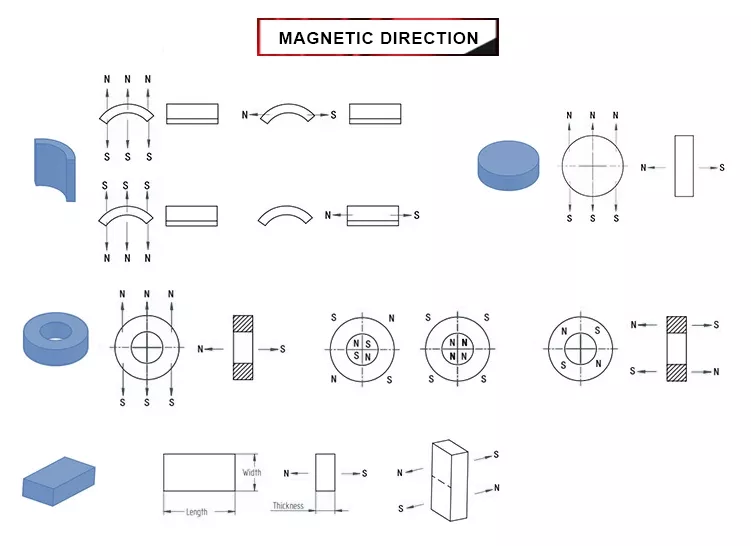
Common magnetization directions are shown in the figure below:
1> Cylindrical, disc and ring magnets can be magnetized radially or axially.
2> Rectangular magnets can be divided into thickness magnetization, length magnetization or width direction magnetization according to the three sides.
3> Arc magnets can be radial magnetized, wide magnetized or coarse magnetized.
Why neodymium magnets need coating ?
Neodymium magnets are incredibly popular due to their powerful magnetic strength. However, these magnets need to be coated in order to protect them and keep them functioning properly. A coating on the surface of a neodymium magnet provides a layer of protection that helps prevent corrosion, wear and tear, and other damage that can occur over time.
Another reason why neodymium magnets need coating is that they are susceptible to corrosion, especially when exposed to moisture or humidity. Over time, this can cause rust or discoloration which can damage the magnet's strength and reduce its effectiveness. By adding a protective coating, the magnet is protected from exposure to moisture and corrosive chemicals, which can help maintain its strength and power.
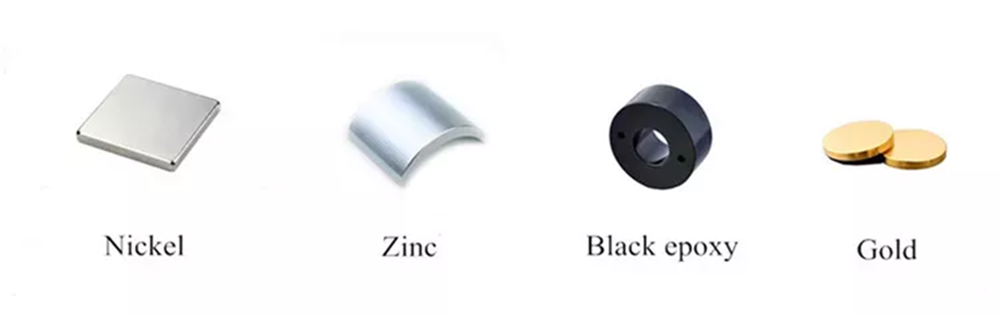
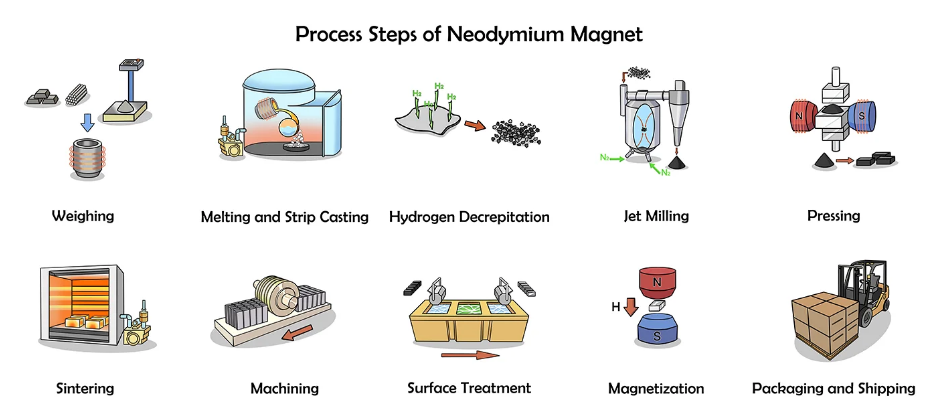
Manufacturing Process
2,The process of creating neodymium magnets starts with the raw materials of neodymium, iron, and boron, which are mixed together in a specific ratio. This mixture is then heated to high temperatures and melted in a vacuum furnace. The molten metal is then poured into a mold, which is usually made of copper, and allowed to cool.
3,Once cooled, the metal is removed from the mold and undergoes a process called hydrogen decrepitation. This involves breaking the metal into small pieces by exposing it to hydrogen gas, which causes the metal to become brittle and fracture. The resulting fragments are then milled into a fine powder.
4,The powder is then mixed with a polymer binder and pressed into a desired shape using a process called injection molding. Once formed, the magnets are then placed in a sintering furnace and heated to a high temperature, which causes the polymer binder to melt and evaporate, leaving behind a solid and dense neodymium magnet.
5,After sintering, the magnets are coated with a protective layer to prevent corrosion and enhance their performance. This can involve plating the magnets with a layer of nickel or other metals.
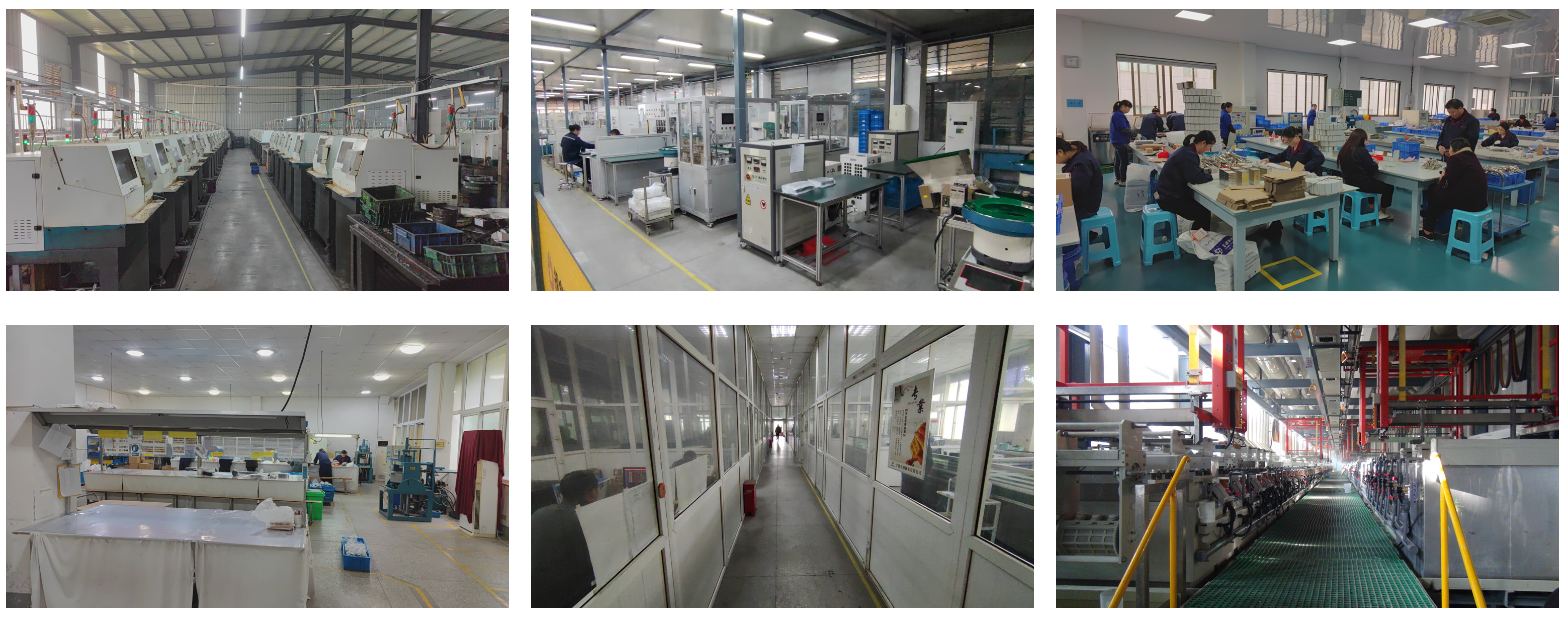
FAQ
Q: Are you trading company or manufacturer ?
A: We are factory.
A: Generally it is 4-7 days if the goods are in stock. or it is 15-30 days if the goods are not in stock, it is according to quantity.
A: Yes, we could offer the sample for free charge if ready in stock but do not pay the cost of freight.
If you have another question, pls feel free to contact us.
Other popular magnets
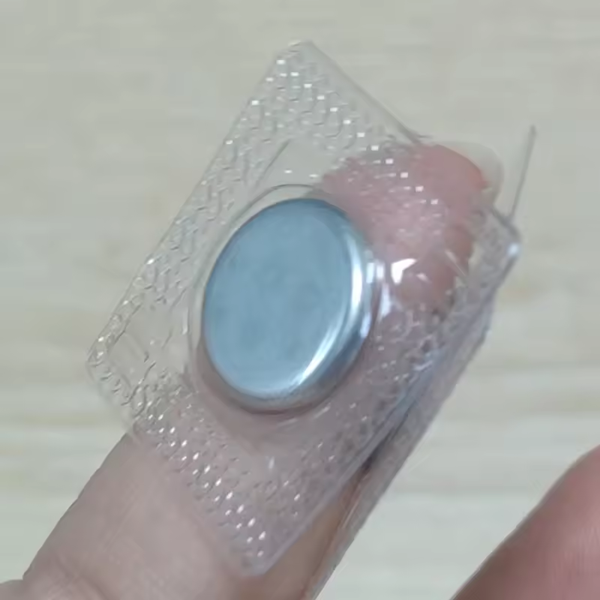
single side neodymium magnet
is commonly utilized in various industries, including wine boxes, tea boxes, gift boxes, bags, leather goods, computer leather cases, clothing, and whiteboard buttons. Its versatility and affordability make it a popular choice for businesses that seek durable and high-quality products.
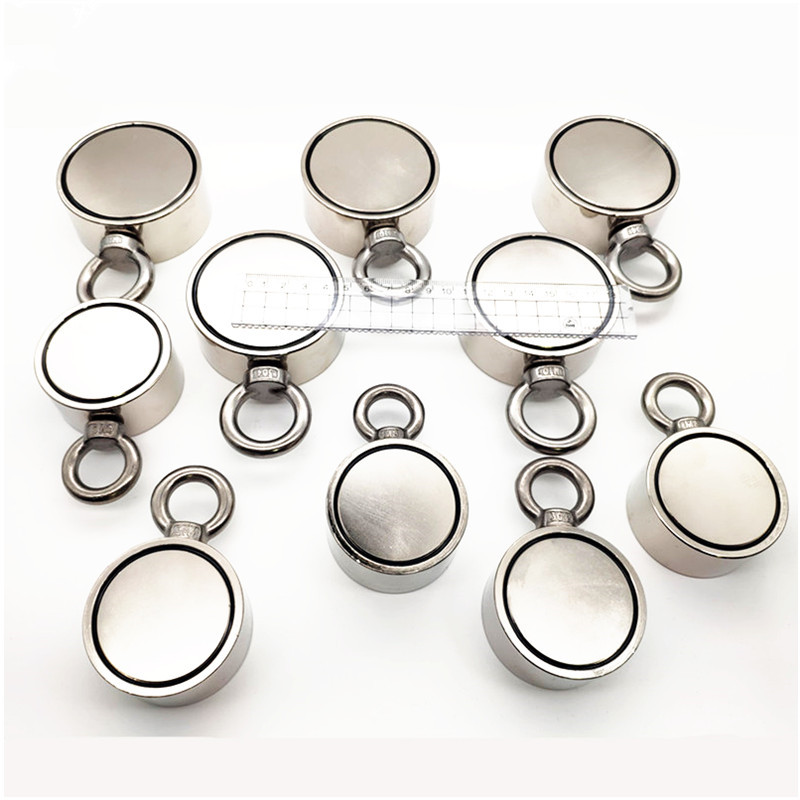
Fishing magnets
are a tool used for magnet fishing, a hobby where individuals use magnets to retrieve metallic objects from bodies of water. These magnets are typically made from neodymium, a rare-earth metal, and are known for their strong magnetic force.