Product Name:
|
Neodymium Magnet, NdFeB Magnet
|
|
Grade & Working Temperature: |
Grade
|
Working Temperature
|
N30-N55
|
+80℃ / 176℉
|
|
N30M-N52M
|
+100℃ / 212℉
|
|
N30H-N52H
|
+120℃ / 248℉
|
|
N30SH-N50SH
|
+150℃ / 302℉
|
|
N25UH-N50UH
|
+180℃ / 356℉
|
|
N28EH-N48EH
|
+200℃ / 392℉
|
|
N28AH-N45AH
|
+220℃ / 428℉
|
|
Coating:
|
Ni, Zn, Au, Ag, Epoxy, Passivated, etc..
|
|
Application:
|
Sensors, motors, filter automobiles, magnetic holders, loudspeakers, wind generators, medical equipment, etc.
|
|
Advantage:
|
If in stock, free sample and deliver at same day; Out of stock, delivery time is same with mass production
|
Neodymium Magnet Catalogue
Form:
Rectangle, rod, counterbore, cube, shaped, disc, cylinder, ring, sphere, arc, trapezoid, etc.
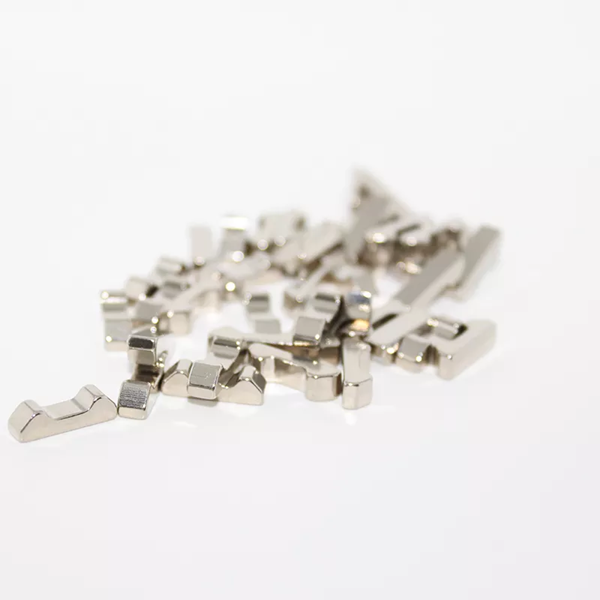
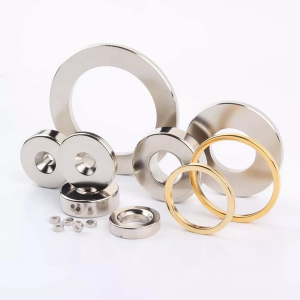
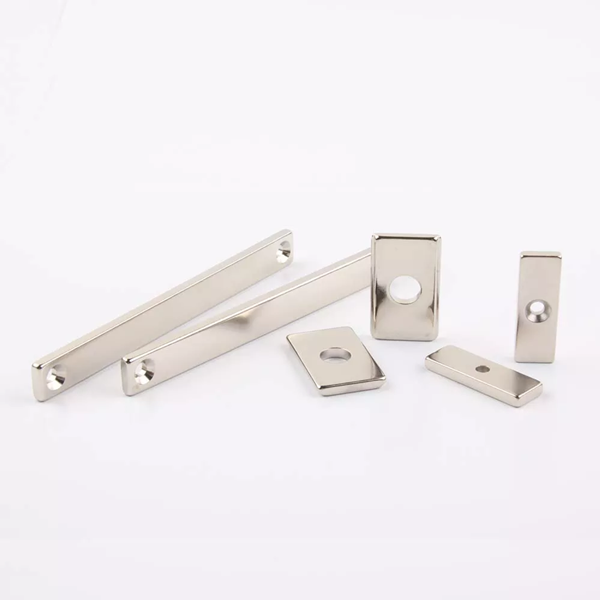
Neodymium magnet series
Ring neodymium magnet
NdFeB square counterbore
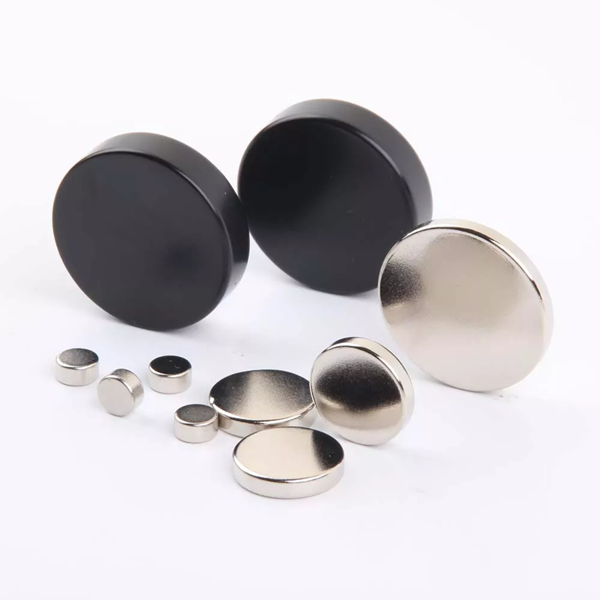
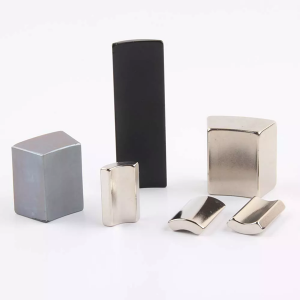
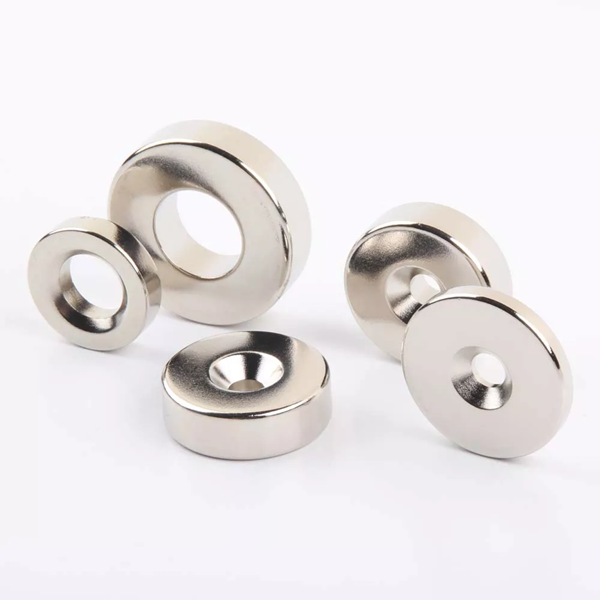
Disc neodymium magnet
Arc shape neodymium magnet
NdFeB ring counterbore

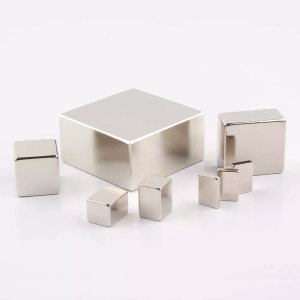
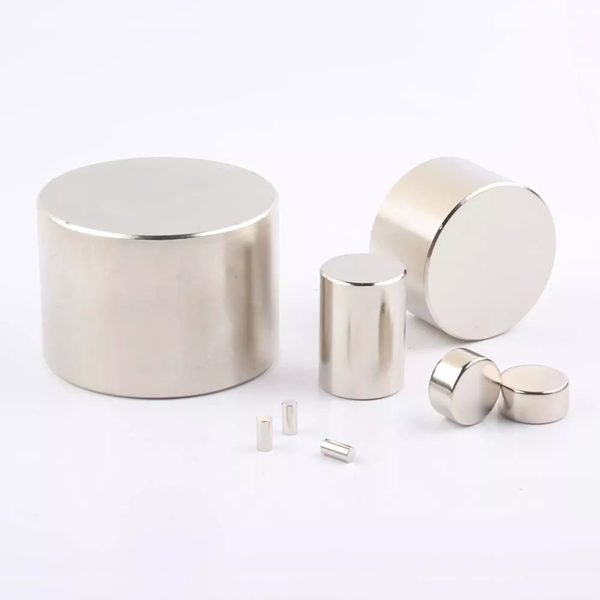
Rectangular neodymium magnet
Block neodymium magnet
Cylinder neodymium magnet
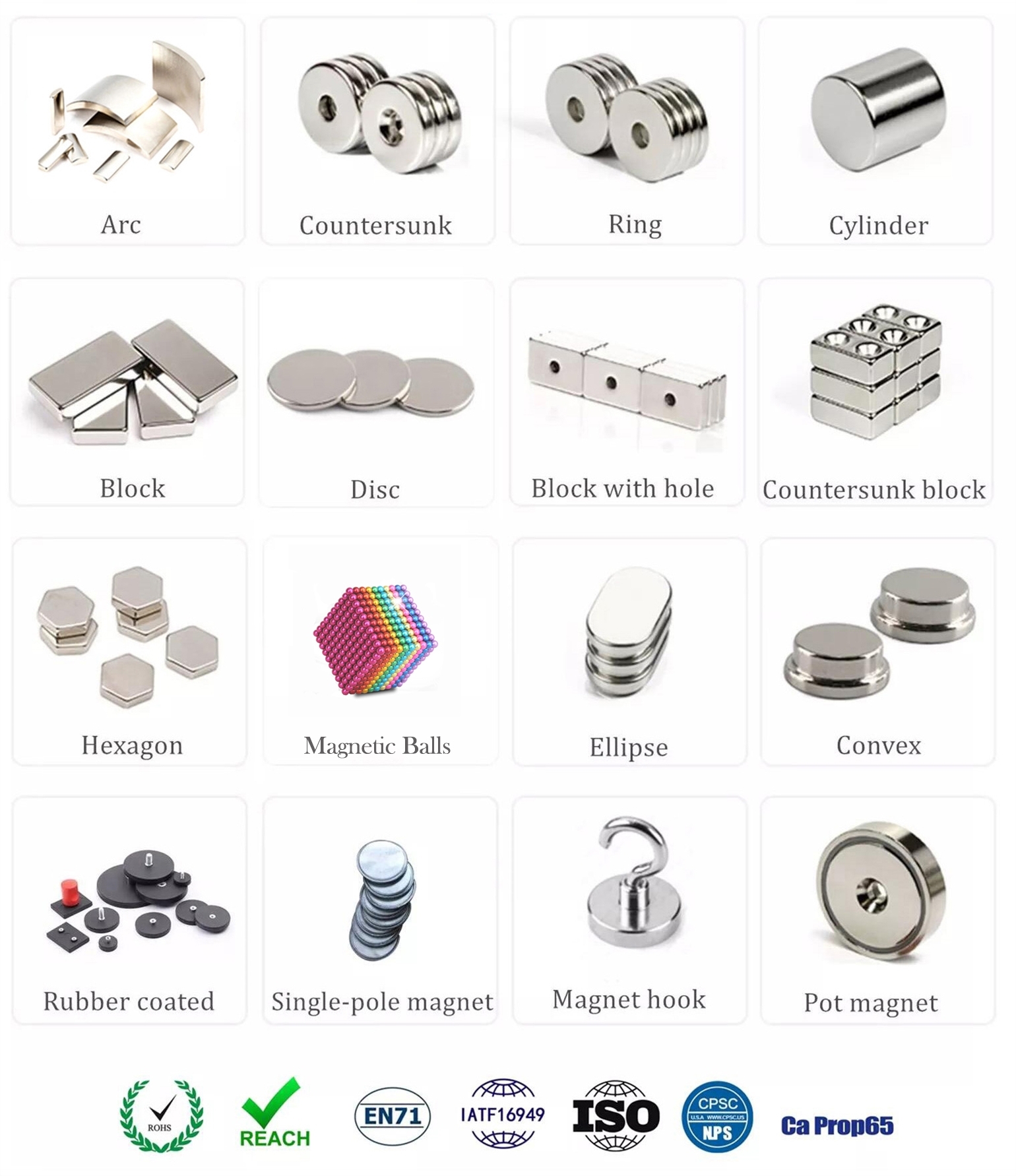
The magnetization direction of the magnet is determined during the fabrication process. The magnetization direction of the finished product cannot be changed. Please be sure to specify the desired magnetization direction of the product.
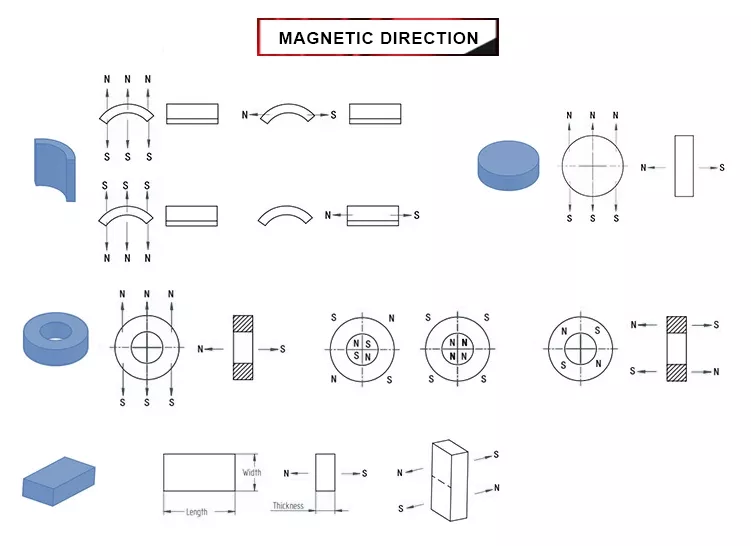
The current conventional magnetization direction is shown in the figure below:
Magnetization direction is the first step for permanent magnet materials such as rare earth iron boron and samarium cobalt magnets to obtain magnetism. It represents the North and South poles of a magnet or magnetic component. The magnetic properties of permanent magnet materials are mainly derived from their easily magnetizable crystal structures. With this deconstruction, the magnet can obtain very high magnetic properties under the action of a strong external magnetic field, and its magnetic properties will not disappear after the external magnetic field disappears.
Can the magnetization direction of a magnet be changed?
From the perspective of magnetization direction, magnetic materials are divided into two categories: isotropic magnets and anisotropic magnets. As the name suggests:
Isotropic magnets have the same magnetic properties in any direction and attract together arbitrarily.
Anisotropic permanent magnetic materials have various magnetic properties in different directions, and the direction in which they can obtain the best/strongest magnetic properties is called the orientation direction of permanent magnetic materials.
Orientation technology is a necessary process for producing anisotropic permanent magnet materials. The new magnets are anisotropic. The magnetic field orientation of powder is one of the key technologies for manufacturing high-performance NdFeB magnets. Sintered NdFeB is generally pressed by magnetic field orientation, so the orientation direction needs to be determined before production, which is the preferred magnetization direction. Once a neodymium magnet is made, it cannot change the direction of magnetization. If it is found that the magnetization direction is wrong, the magnet needs to be re-customized.
Coating and Plating
Due to the poor corrosion resistance of NdFeB magnets, electroplating is generally required to prevent corrosion. Then the question comes, what should I plate the magnets for? What is the best plating? Regarding the best effect of NdFeB coating on the surface, first of all, we should know which NdFeB can be plated?
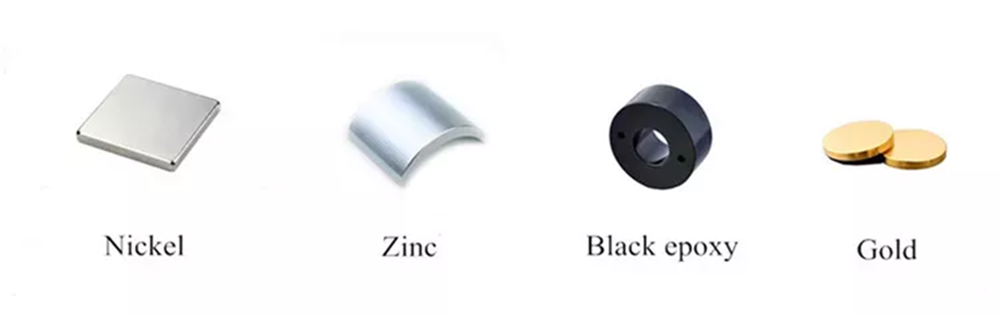
What are the common coatings of NdFeB magnets?
NdFeB strong magnet coating is generally nickel, zinc, epoxy resin and so on. Depending on the electroplating, the color of the magnet surface will also be different, and the storage time will also vary for a long time.
The effects of NI, ZN, epoxy resin, and PARYLENE-C coatings on the magnetic properties of NdFeB magnets in three solutions were studied by comparison. The results showed that: in acid, alkali, and salt environments, polymer material coatings The protection effect on the magnet is the best, the epoxy resin is relatively poor, the NI coating is second, and the ZN coating is relatively poor:
Zinc: The surface looks silvery white, can be used for 12-48 hours of salt spray, can be used for some glue bonding, (such as AB glue) can be stored for two to five years if it is electroplated.
Nickel: looks like stainless steel, the surface is difficult to be oxidized in the air, and the appearance is good, the gloss is good, and the electroplating can pass the salt spray test for 12-72 hours. Its disadvantage is that it cannot be used for bonding with some glue, which will cause the coating to fall off. Accelerate the oxidation, now the nickel-copper-nickel electroplating method is mostly used in the market for 120-200 hours of salt spray.
Production Flow
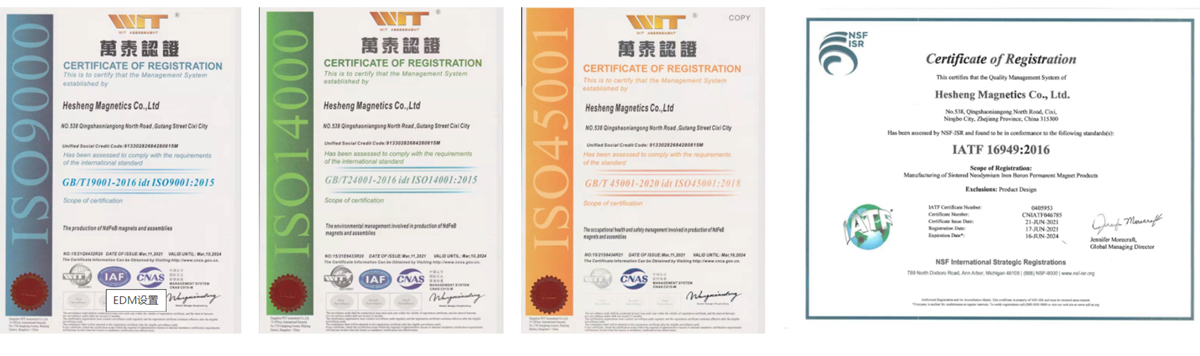
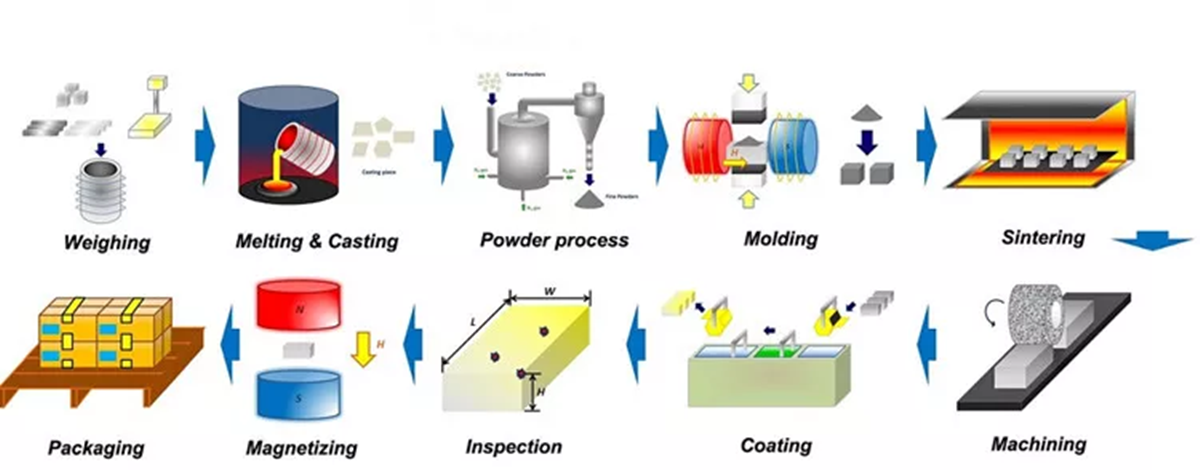
Packing
Packaging details: magnetically insulated packaging, foam cartons, white boxes and iron sheets, which can play a role in shielding magnetism during transportation.
Delivery details: Within 7-30 days after order confirmation.
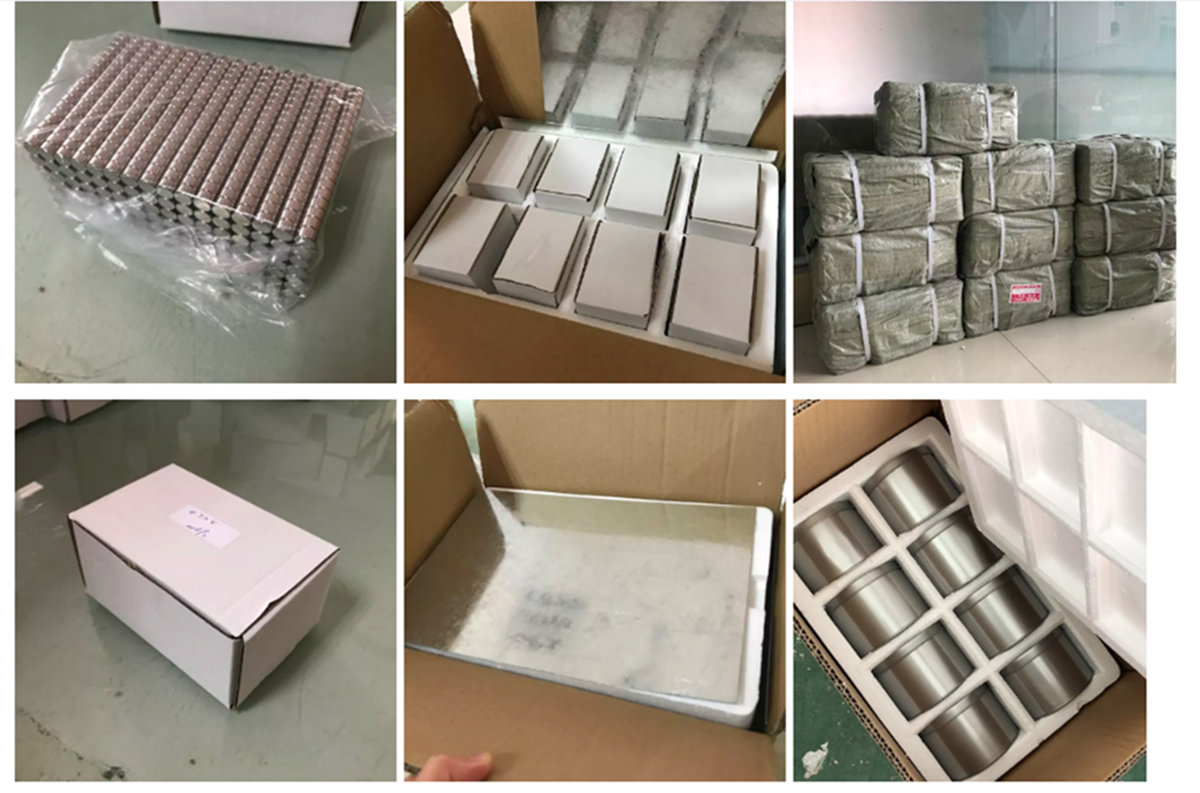
FAQ
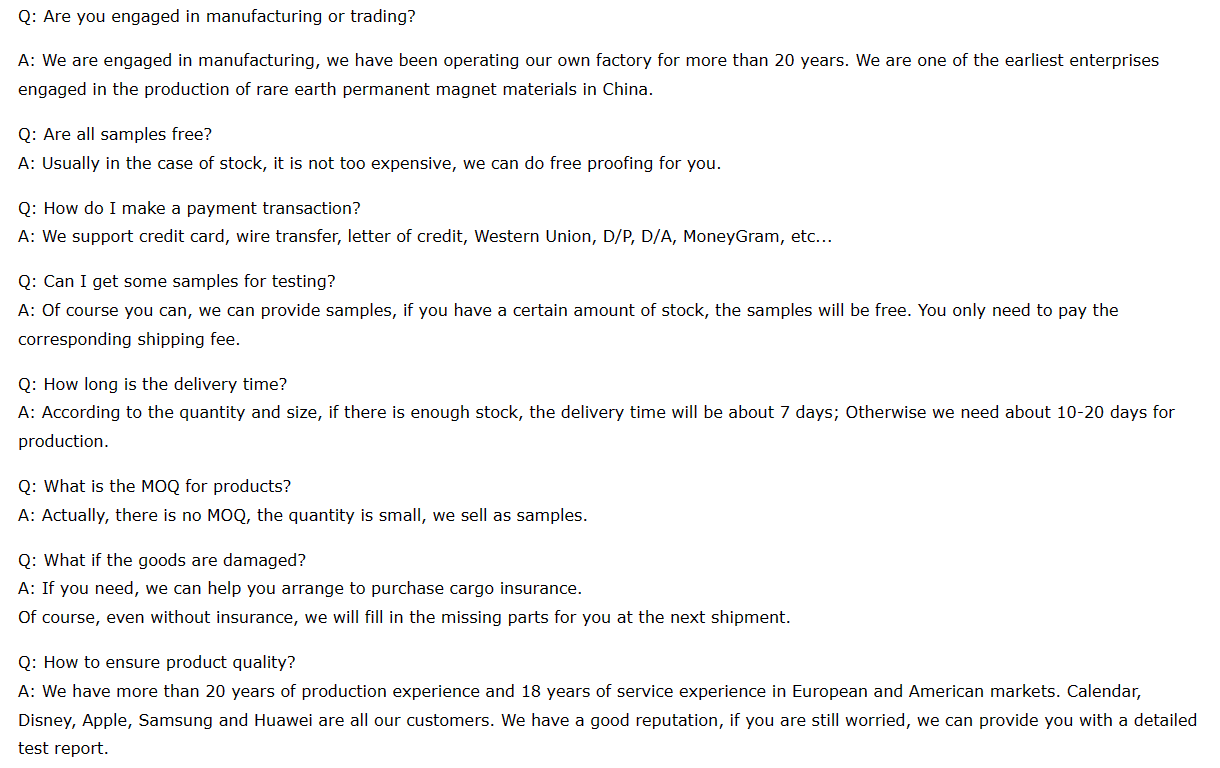
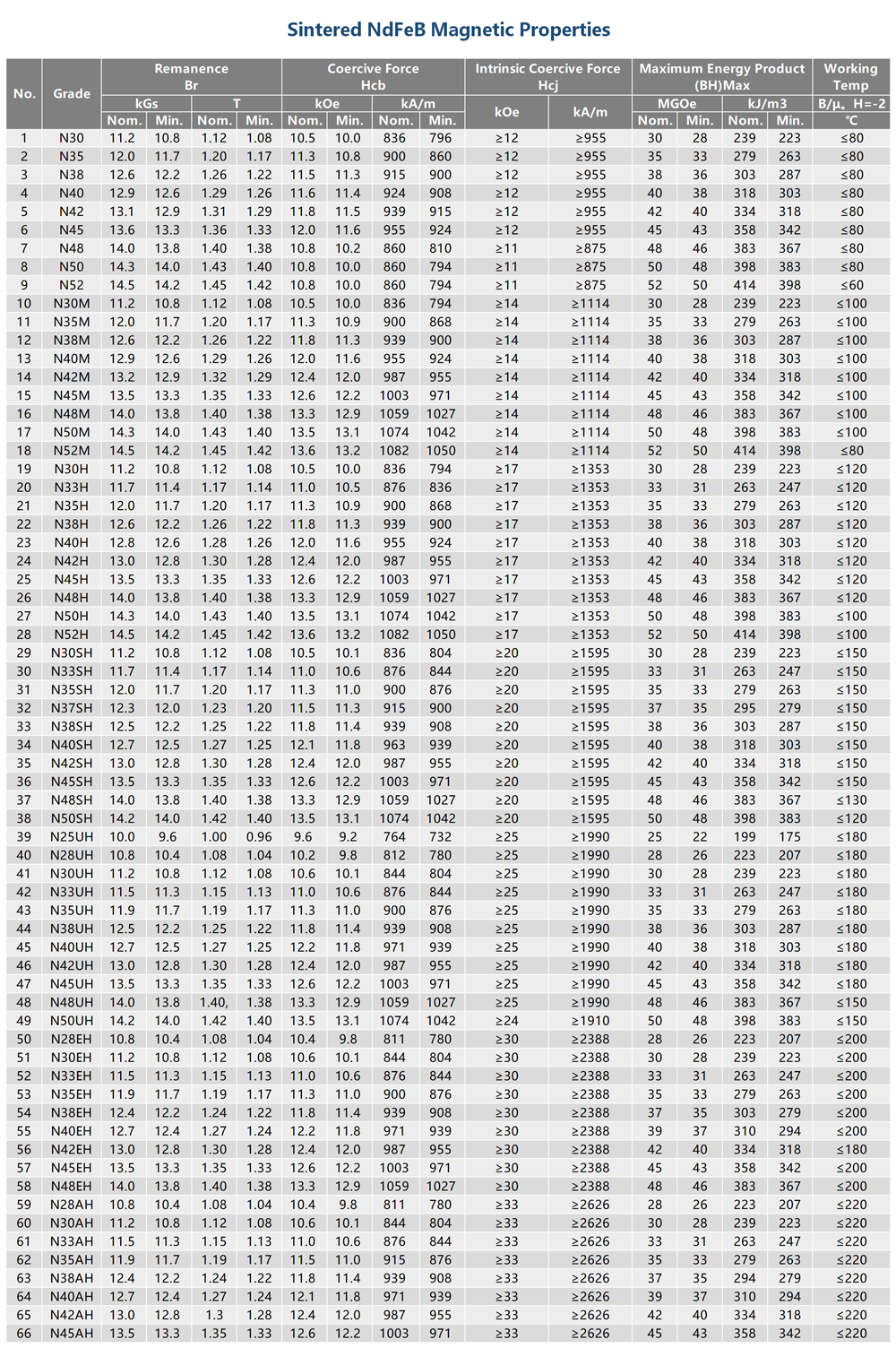